Parylene is used in medical, aerospace, military, and almost every other industry we can think of. Its applications are as varied as its benefits and have an impressive list of advantages over other conformal coatings. Taking an even closer look shows that the different types of parylene have their own unique benefits. Each of the three types is best for a certain kind of job.
Here we'll cover the three types of parylene—N, C, and D—the benefits of each, and what sorts of projects you might use them for.
3 Parylene Types: N, C, & D
If you're seeking to learn more about parylene, odds are you've heard a little bit about its more common uses. (Unless you find parylene's uses and composition fascinating, which, we'll admit, we do). Some of the most common place usages you've likely run into would be:
Parylene is a diverse, efficient type of coating that has been developed to fit into and benefit our modern world in many different ways.
There are three parylene types used on various mediums that need protection. Let's take a look at them next.
Parylene N
Parylene N is a common and widely used conformal coating. Often considered a basic type of coating because there are many applications of the product. Parylene N has a melting point of 420°C (or 788°F), has a unique vacuum stability, and has proven very useful in applications of high frequency.
Parylene C
Parylene C is highly resistant to corrosive gasses, moisture, vapor, and various chemicals. The coating can protect products for up words of 10 years in extreme environments. Because of these characteristics, Parylene C is used for most products that need a conformal coating for protection.
Parylene D
Parylene C and D are very common in characteristics. However, Parylene D has a slightly higher temperature tolerance. This coating provides reliable assembly protection at 100°C (commonly known as the point at which water boils), in oxygen-dominated areas.
Benefits of Parylene C, N, & D
There are different benefits to each of these polymers, as explained below:
- Parylene C - parylene C has proven itself to be incredibly useful, boasting an impressively low permeability to moisture, corrosive gases, and chemicals.
- Parylene N - parylene N is a wonderful option when a more intense coat of protection is important to your use of the polymer. Its constants don't react when there are changes in frequency.
- Parylene D - this type of parylene does well under pressure. Whether we're talking physical strength or original electrical properties, parylene D holds itself up under higher temperatures.
All three of these polymers have revolutionized the conformal coating industry. That's why Advanced Coating exists today.
Now let's look at what are the key benefits of Parylene Coating and why it is considered to be one of the best forms of protection for the surface of electronic devices.
Key Benefits of Parylene Conformal Coating
There are several key benefits of parylene, including its non-liquid nature, versatility, resistant properties, and chemical inertness. Let's take a closer look at each of these.
Non-liquidity
The film is liquid-free, therefore making it safe on even the most sensitive electronics. It is also extremely thin, so it can still act as a liquid in that it can fit in small crevices without possibly damaging effects.
Versatility
Obviously, being non-liquid makes it extremely versatile. In addition, Parylene Conformal Coating has been approved for use on a variety of things, such as:
- Conformal Coating For Circuit Boards & Electronic Assemblies (Meets MIL-I-46058C, Type XY)
- Particle Immobilization (e.g. Disk Drive Metal Components)
- Lubricity (e.g. Catheter Guide Wires)
- Dielectric (e.g. Cores/Bobbins)
- Hydrophobic (e.g. Biomedical Tubing)
- Barrier (e.g. Filters, Membranes, Valves)
Along with being able to coat particular products, it can also be used on paper, glass, metal, plastic, ceramic, and other surfaces.
Resistant Properties
The film's resistant properties make it an effective barrier against thermal damage, as well as resistant to chemical attacks.
Chemically Inert
Due to its chemically inert property, parylene has been approved by the Federal Drug Administration (FDA) to be utilized on implantable devices. This assists in maintaining the devices within the body for longer periods of time.
As you can see, Parylene Conformal Coating provides several exceptional benefits for a variety of different products and uses. With its non-liquid properties, versatility, and strength, it is the perfect choice for your coating needs.
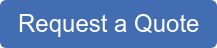
Why Use Parylene Conformal Coating?
Now that we have covered what Parylene conformal coating is, the three main types and their characteristics, let's look at why you should use parylene over other conformal coatings.
- Protection. Each type of parylene protects against extreme heat, cold, corrosive gases, vapor, and moisture. These are all highly valuable benefits in the real world of aerospace, medical devices, and military equipment. When considering what coating to use, you must take into account what level of protection is needed against harsh environments and extreme conditions without sacrificing functionality.
- Control. In order to reap the benefits of any coating used, control during the application process is crucial. Controlling the thickness and placement is easy to control in the dimer processes.
- Conformity. Parylene conforms even to surfaces without pooling, bridging, or spotting. Since parylene is applied while it is in a gaseous state, it can adhere to unusually shaped surfaces and reach small crevices.
Most Common Uses of Parylene Conformal Coating
Circuit Boards
This particular coating possesses several characteristics that make it perfect for circuit board usage. Some of the main qualities include:
- Thin enough to fit into areas as small as 0.01mm
- Conforming to fit seamlessly on any surface
- Resistant to fungus and other deteriorating properties
Rubber and Plastics
Being that the parylene coating is so versatile, it is the ideal coating for rubbers and plastics that need to maintain their flexible properties. The film is able to bind to the plastic securely to provide exceptional coverage.
Medical Devices
Parylene is chemically inert, which makes it safe to use on medically implanted devices. Its resistant qualities also help to maintain the devices in the body longer.
Glass and Windows
The thermal-resistant coating proves to be the perfect film to protect glass and windows as they must brave intense elements.
Conclusion
Parylene is used in medical, aerospace, military, and many other industries. Its applications are as varied as its benefits and have an impressive list of advantages over other conformal coatings. Taking an even closer look shows that the different types of parylene have their own unique benefits. Each of the three types is best for a certain kind of job.
Want to learn more about how Advanced Coating can help with all your coating needs?