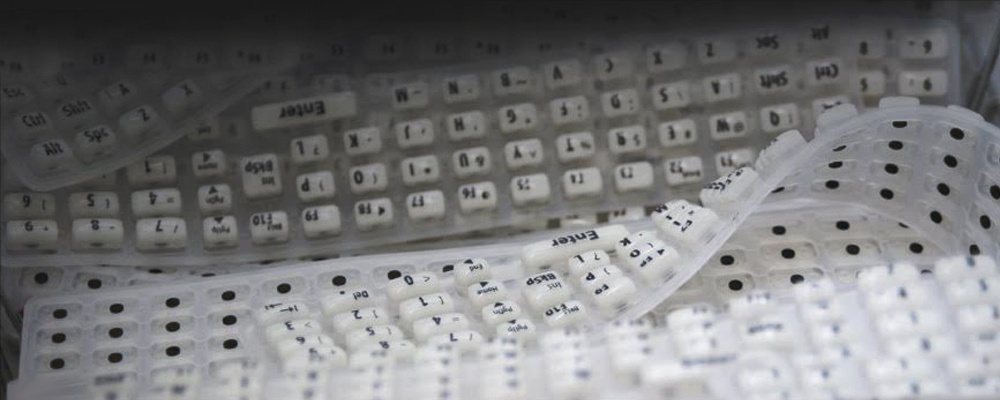
Where can Parylene be used?
Conformal coatings, particularly Parylene, are everywhere. From deep sea submersibles to spacecraft to traffic light internals to pacemakers and stents internal to the human body there are conformal coatings at work. If your application needs electrical, biological or environmental protection, there is almost certainly a conformal coating suitable to the task. Examples include:
- Articulated medical device assemblies
- Balloons
- BGA's
- Bobbins
- Cannulas
- Catheters
- Chips
- Complex shapes
- Ferrite Cores
- Ferrite parts
- Fiberglass/resin
- Flex cables
- Grommets
- Keypads
- LED's
- Load cells
- Magnets
- Mandrels
- Metal; iron, steel, brass, copper, aluminum, spun copper, brass, nickel, et al
- Motor housings
- Needles
- Nitinol
- O-rings
- Pacemakers
- Paper
- Plastic
- Poppets
- Powdered metal
- Printed wiring assemblies
- Probes
- Shapes with internal voids
- Silicon wafers
- Springs
- Stators
- Stents
- Stirring rods, balls, discs, paddles, et al
- Tubing
- Wood
What You Need to Know
Before the application process ever begins, there are a few prerequisites that must be taken care of--and they're incredibly important. These include details like the desired coating thickness, the safety standards that must be met depending on the industry and usage, and the areas on the substrate surface that must not be coated. All of this information must be gathered before the coating process so that everything goes smoothly and there's no need to stop or redo any work.
There are three common application methods used by many conformal coating companies. Each has benefits and drawbacks to consider.
- Brushing. The first method of liquid application is called brushing and is generally used for small jobs or repair. It tends to be slower, does not offer options for carefully managing thickness, and the quality of the coating relies on the precision and skill of the operator.
- Spraying. Spraying is a strong choice for more intense jobs because it's more reliable. It can be applied at carefully managed thicknesses and creates a strong, reliable coating. However, substrate cleanliness is absolutely crucial for success.
- Dipping. The final and most common method of liquid application is dipping, a fast and reliable option in which the substrate material is dipped in the coating. It can be used for high-volume jobs and, while it demands some extra care, does provide a reliable coating.
Check out our application guide for more info or contact us today to get started.